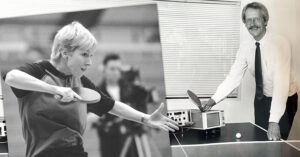
Our 40-year history:
table tennis
Why is Comtest Engineering founder Hein de Groot holding a table tennis bat in this 1988 photo? This year, we are celebrating our 40th anniversary, and every five weeks, we share a bit of Comtest’s history.
Dirt on your test chamber doors can cause serious performance issues, leading to unnecessary costs, downtime, or even non-compliance. For tempest-shielded facilities, it could even lead to a security breach. Our colleague Joëlle Driessen-Verkuijlen, who oversees our maintenance contracts, explains these risks and has a simple solution.
Joëlle: “When dirt, like the visible kind in the photo, increases on your test chamber’s door knives, they cannot connect properly with the frame’s finger stocks. In that case, the chamber is not fully closed off, which creates the risk of RF leakage. Additionally, if this dirt is not removed on time, it can accumulate behind the fingerstocks, requiring extensive maintenance and potentially the removal and replacement of these door parts. And that leads to downtime of the chamber.”
How can it come this far?
Joëlle: “Not all clients add yearly maintenance agreements to their new Comtest chamber, while that would solve these problems easily. Some say they do not use the chamber that often and do not see the need for yearly maintenance. But the dirt is not coming from the chamber, but from space around where people walk by daily or after an internal renovation, when dust is formed.”
How does the maintenance program work?
Joëlle: “With our current clients, I first look at last year’s report with data on the battery’s condition and the fingerstocks. Then, I create a maintenance proposal for the client based on the previous year’s information, plan for a maintenance specialist, and order the necessary parts for him to bring with him. The Faraday cage is checked for performance during the visit, and the doors are thoroughly inspected and cleaned.
For new clients with a chamber we have not inspected, it is more challenging to determine which parts are necessary, which increases the risk that my colleague will have to return. My colleague, Edwin Van Der Ploeg, is preparing to provide in-house training for our clients, enabling them to manage simple maintenance themselves. Currently, it is in a trial stage, but it can help our clients understand that regular maintenance is essential, regardless of who performs it. However, remember that our five-year warranty requires an annual inspection by us.”
You can prevent downtime in your testing chamber caused by neglected maintenance by contacting Joëlle Driessen-Verkuijlen to discuss your options. It’s better to be safe than sorry…